FLEXIROHR METHOD
Renos Flexipipe is a trenchless sliplining method specifically designed for the renovation of gravity sewers with diameters between 100 and 300 mm. Flexipipe is a pipe with a ring stiffness classification of SN8 (the 270 mm Flexipipe is classified as SN4), suitable for demanding conditions, offering durability and a long service life. In this method, a new continuous pipe is installed between manholes without joints, minimizing the risk of leaks and preventing, for example, root intrusion into the sewer line. The advantage of the method is that the new pipe can be installed inside the old sewer without excavation, making it a quick, environmentally friendly, and cost-effective solution. During the Flexipipe installation, the sewer remains operational, and no interruptions or bypass pumping are required.
The installed Flexipipe product has the smallest carbon footprint on the market (LCA A1-A5). This is due to both the energy efficiency of the sliplining process and the durability, longevity, and optimized design of the materials used. Less raw material and energy are consumed as the old pipeline can be renovated without the need for trenches or the transport of large quantities of soil. All of this makes Flexipipe sliplining an environmentally optimal way to rehabilitate gravity sewers.
Compared to CIPP (cured-in-place pipe) lining, where the liner is cured underground, the installation of factory-manufactured Flexipipe is significantly less risky. Flexipipe is manufactured according to the high-quality standards of the factory and welded on-site to the required length. The liner, in contrast, is produced under job site conditions, where issues such as uneven curing of the liner may occur, potentially affecting the product’s quality and longevity. The installation of Flexipipe does not involve chemicals, such as the resin used in CIPP lining for curing, which reduces environmental and health risks. This makes Flexipipe a safer option for both installers and the environment, ensuring a consistent and reliable result without chemical emissions or uncertainties related to the curing process.
ADVANTAGES AND BENEFITS OF THE METHOD
- Factory produced pipe (SN8 or SN4) means a long-lasting solution, lifetime over 50 years
- Tight, continuous, welded system without digging
- Sewer can be functional during installation means no bypass needed
- Fast and efficient installing means less harm to traffic and the citizens
- welded to exact lengths for each section means no waste
- corrugated pipe structure means lower usage of oil and lower weight
- No toxic waste
- Pull-resistant couplings
ADVANTAGES FOR THE INVESTOR
- a long-lasting solution lifetime over 50 years
- an efficient method means competitive price level
- efficient installing means little harm to traffic
- the advantages of polyethylene, a known material in the industry
ADVANTAGES FOR THE INSTALLING COMPANY
- low risk in installation, means more turnover, less claim costs
- small amount of equipment, fits in a van, means better return on investment
- low initial investment, better return on investment
- easy installation means less operating costs
- installation possible in the winter => all-year operation
- no chemicals in the installing process, better health & safety
- training and sales support available
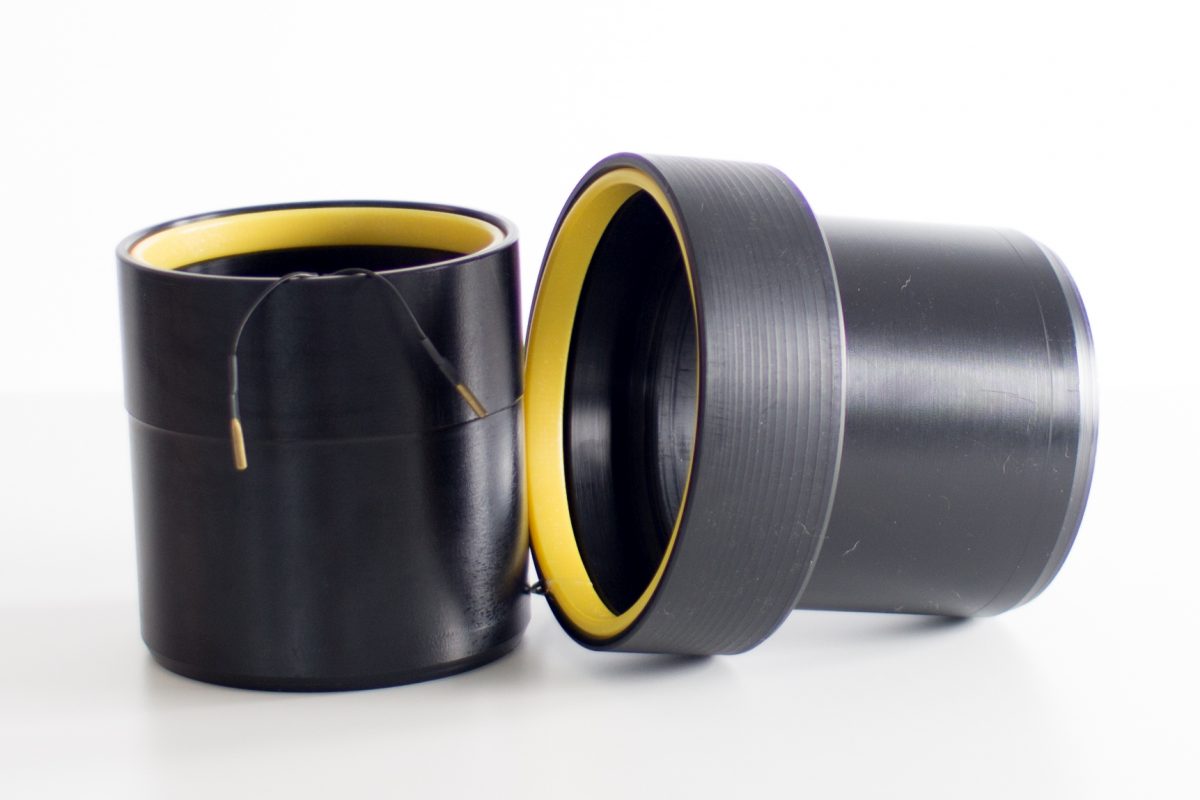
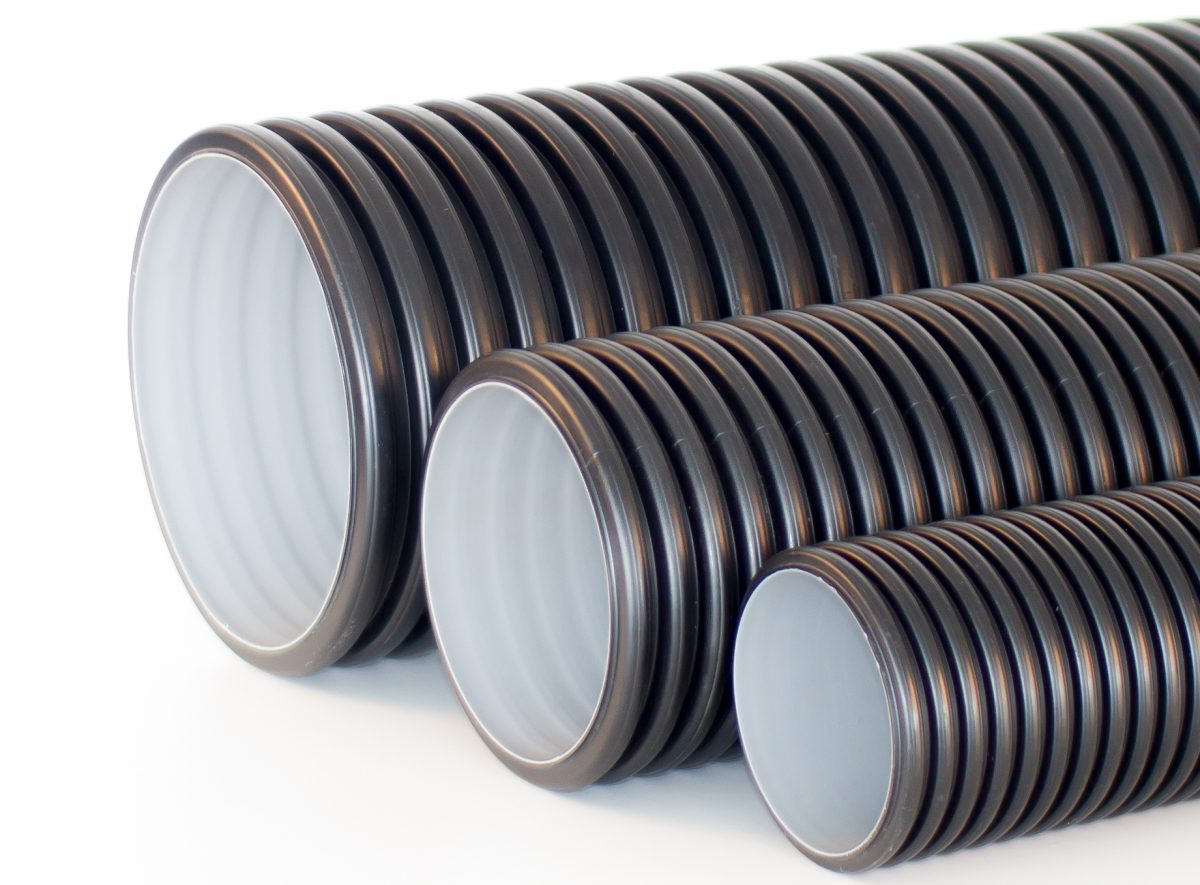
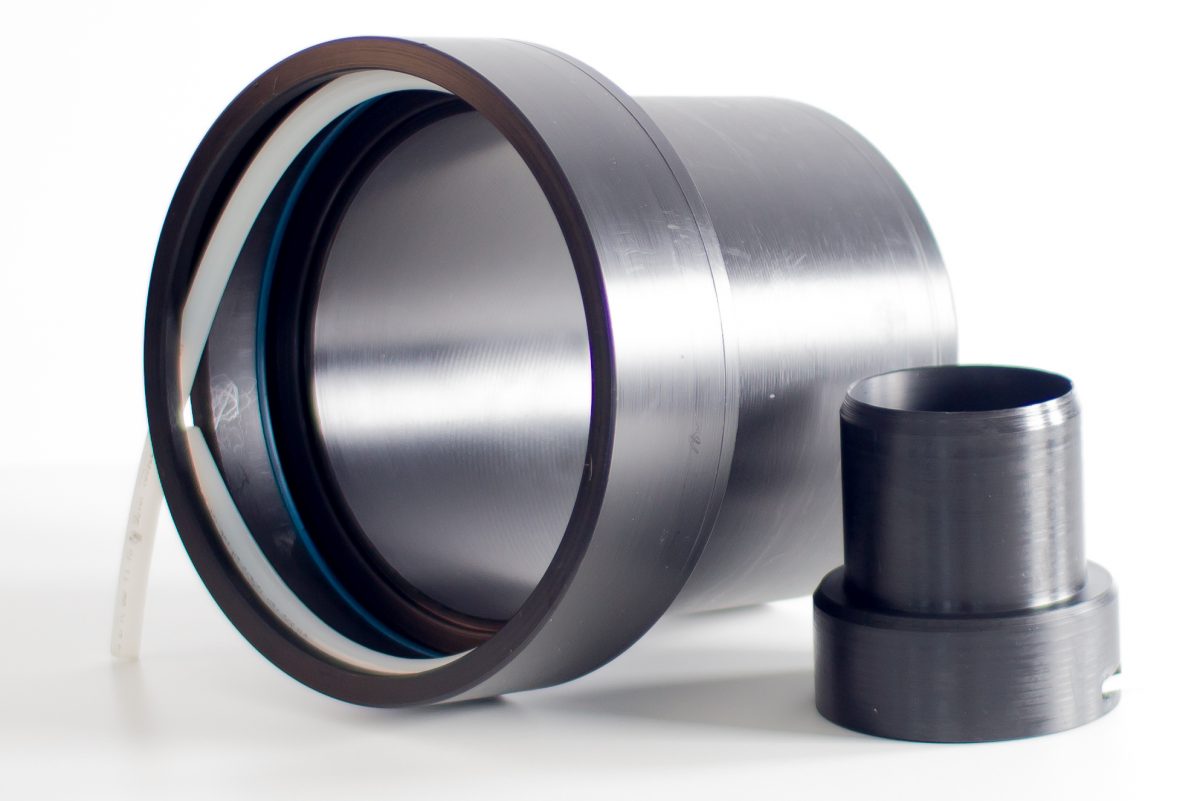